PCB Manufacturing at my university (Pictures)
December 19th, 2008So I etched a PCB at my university today, and i thought I’d share some pictures. Today’s PCB is an XR-2206 Based Voltage Controlled Oscillator, a rad oscillator synth module.
The manufacturing process involves several transfers: Paper -> Photographic film -> Photoresist -> Copper. Let’s begin with a picture of three of the steps, the printed paper, the film and the finished PCB.
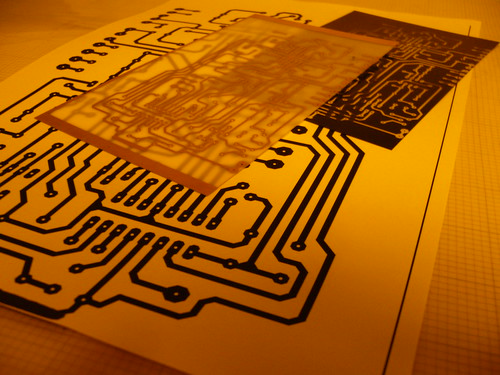
So the first thing I have to do is print the layout on paper. It needs to be printed with high contrast and dense blackness to transfer well to the photographic film. For this PCB I chose to do the transfer double sized to increase the contrast, but you can transfer it with a 1:1 size source printout. (Or anything between)

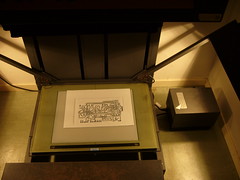

When you press a button, two light sources are turned on to expose the film. The light is reflected against the source material through a lens, and onto the film. The film is, as far as I know standard black and white photographic film. In other words, this device is a giant camera.
The next step is to develop the film. This is done by putting the film first in a “developer” fluid to make the image visible, and then in a “fixer” fluid to protect the film from light. Until the film has been completely developed, the photo room must be lit strictly using a faint red light to avoid exposing the film by accident.


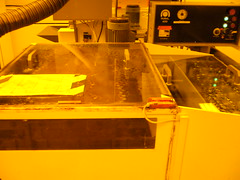


Almost done. The last step is to put the board into a stripper fluid (NaOH, Sodium hydroxide) to remove the remaining photoresist.
After drilling the holes the PCB is ready to be equipped with components.
April 15th, 2013 at 8:35 pm
Hi I am Baker from Jordan
well your steps is normal , the same I do but if you tell me
why you use CaCo3 befor etching
and why you use Iron chloride instead of ferric chloride ?
is it stronger ?
I do not use calcuim carbonate ..is it necessary for good result?
April 15th, 2013 at 8:56 pm
Hello. This depends on which method you use. This method is using a protective layer (photoresist) which is hardened by light. This is done with UV light. When you apply CaCO3, the part of this layer that is soft will be removed, but the part of the layer that is hard will stay.
If you are using a different method, you need a different chemical than CaCO3. CaCO3 is only for the photoresist method.
Iron chloiride is the same as ferric chloride. Different names.
March 26th, 2019 at 8:27 am
[...] See also GameBoy genius’s page PCB Manufacturing at my university (Pictures) [...]